Game-changing distribution blocks for the mobile market
Global provider of automation connectivity and control devices introduces first of its kind “xtreme DB” using Deutsch connectors.
Murrelektronik, the global automation systems component provider announced today the availability of a distribution block designed to deliver more power and better performance to the mobile vehicles market. Designed with ports for Deutsch connectors, the new xtreme DB provides up to three times the current carrying capacity compared to blocks of similar size, along with design efficiencies that will help to transform the way control systems are developed by heavy-duty vehicle builders.
“The xtreme DB is a game changer,” said Jon Halton, President of Data Panel, the Murrelektronik subsidiary that developed the block. “In one block you get a higher current rating, more I/O ports and stronger, more reliable power distribution with Deutsch connectivity.”
xtreme DB blocks with Deutsch connectors have eight I/O ports and 16 configurable outputs and can do the work of multiple ordinary blocks using standard M12 connectors. As an example, in one competitive application for the rail industry, the number of blocks required would drop from 20 to 12, with an accompanying reduction in harness size, shorter cable runs and improved serviceability.
“We’re delivering major quality and performance improvements in a versatile solution that will change how control panels are developed for specialty vehicles. I’ve never been more excited to introduce a new product,” said Kristian Gullikson, Murrelektronik’s manager for mobile business development.
The xtreme DB is specifically designed to meet the power distribution needs of heavy-duty vehicle manufacturers who build agricultural machines, railway and construction equipment, trucks for fire and rescue, road and utility maintenance, garbage collection, and other mission specific vehicles.
Murrelektronik’s xtreme DB offers the push and lock dependability of Deutsch connectors in contrast to M12 connectivity, which can be prone to weak or loose connections in harsh locations. Deutsch connectors are specifically designed for critical applications in harsh environments where dust, dirt, moisture, salt spray, and rough terrain can contaminate or damage electrical connections and systems. The xtreme DB is available in five configurations and utilizes J1939, the standard communications network for sharing control and diagnostic information between electronic control units on heavy duty and commercial vehicles.
Interested in learning how xtreme DB can help you? Contact Price Engineering at 262.369.3700 today!
Mega trends and fluid power
Tom Price Jr. was a keynote presenter this year at the Fluid Power Technology Conference. His focus was on the future and sustainability of fluid power.
Most of us focus on our latest project or deadline with a “nose-to-the-grindstone” mentality. It’s also worthwhile to occasionally step back and look at the big picture, says Tom Price, president of Price Engineering. In his keynote presentation at Fluid Power World’s recent Technology Conference in Milwaukee, he pondered some mega trends affecting society, and what they mean to the fluid-power industry.
Read the entire article at Fluid Power World.
Are you ready for electro-hydraulic implementation?
Fluid Power Journal spoke with Price Engineering owner, Thomas Price Jr. to discuss the recent growth in the integration of electronics and hydraulics.
The integration of electronics and hydraulics has grown dramatically in recent years, but not everyone has jumped on the bandwagon. For those considering implementing electro-hydraulic (EH) solutions, the key question often boils down to: “How do you know when you’re ready?” To answer that question, those considering EH implementation should consider the benefits available, evaluate areas that can best capitalize on those benefits, and develop a game plan for implementation.
Read the entire article in Fluid Power Journal.
Experience the Power of X20
Small Pump. Big Power.
Around the world, engineers are leveraging Eaton X20 open-circuit piston pumps to get better power density in their mobile equipment. The reliability, productivity and efficiency of these small, lightweight pumps makes them an ideal solution for a wide range of medium pressure mobile equipment – including Tier IV applications.
Drive Fuel Efficiency.
Known for providing stability and fuel efficiency in a variable speed fan drive system, the X20 portfolio of products is typically used in the construction, mining, agriculture and on-highway market segments.
Product Features
Keep operations up and running
- Robust, simple design with fewer parts
- Unique control piston design that minimizes friction Long bearing life
- Case to inlet check valve to reduce pressure spikes and protect the shaft seal
Maximize power for a more efficient pump
- Low pump stand-by pressure (~150 psi) enables energy savings by reducing heat generation and wasted flow
- Optimized valve plate design
- Bronze shoe design that stands up against contamination
- Compact package size to fit with Tier 4 engine requirements
Get the job done faster
- Fastest response and recovery times in the market
- High horsepower capability
X20 controls offering
- Pressure Control limits outlet pressure to a set maximum
- Load Sense limits outlet pressure to a set margin above load pressure
- Cold Start forces pump to near-neutral when electrical current is applied
- Torque Control limits pump torque to a set maximum
- Remote Pressure Control limits outlet pressure proportional to signal pressure. It’s ideal for applications where frequent system pressure adjustment is required due to workload requirements.
- Fan Drive Control limits outlet pressure negatively proportional to signal current. Performance benefits include great control stability, higher max pressure setting, and the wider pressure setting range.
Interested in being part of the X20 experience?
Contact us to learn how you can have an X20 prototype expertly installed for free!
Blowing past conventional thinking about reservoirs
Price Engineering has developed a new range of hydraulic reservoirs designed to be as much as 90% smaller and lighter than conventional hydraulic reservoirs. The Cyclone Hydraulic Reservoirs are engineering fro mobile hydraulic systems up to 100 GPM.
Read the full article from Diesel Progress.
Hartland firm says it’s shaking up hydraulic fluid power industry
A Hartland firm says it’s stepping up technology aimed at making big machines, such as garbage trucks and construction equipment, more efficient and better for the environment.
Price Engineering made its announcement Tuesday at a fluid power technology conference that continues Wednesday, from 8 a.m. to 5 p.m., at Milwaukee School of Engineering.
Price says it’s collaborated with Solar Plastics, of Delano, Minn., on the development and manufacture of new hydraulic fluid systems that, in some cases, reduce the amount of toxic, mineral-based fluid used by more than 90%.
See the entire article at the Milwaukee Journal Sentinel.
New Hydraulic Reservoir Revolutionizing Fluid Power Industry
Modern design can be 10-20 times smaller than traditional reservoirs
Hartland, Wis. – Price Engineering of Hartland, WI and Solar Plastics of Delano, MN, have collaborated on the development and manufacturing of new hydraulic reservoirs that are certain to revolutionize the industry. Sized 10 to 20 times smaller than traditional hydraulic reservoir systems, the new Cyclone Hydraulic Reservoirs require less fluid volume, reduces weight, diminishes air and occupies a smaller space. The new Cyclone Reservoirs will officially be unveiled at the Fluid Power Technology Conference being held at Milwaukee School of Engineering’s Kern Center, June 21-22, 2016.
“Hydraulic Reservoirs, which are used to power anything from machine tools to garbage trucks, really haven’t changed much in design over the past 30 years. The new Cyclone Hydraulic Reservoirs are noteworthy because they are so much smaller than the traditional Reservoir,” says Terry Glidden, managing director at Price Engineering.
“They can be sized smaller because they dissipate air more rapidly. The technology removes suspended air from the hydraulic fluid with cyclonic action. The strong rotational movement within the Cyclone Reservoir creates centrifugal forces which combine, and push, air bubbles to the center of the reservoir, and eventually, out the reservoir via what we call a breather cap.”
Sam Rosen, vice president of sales at Solar Plastics says, “Many original equipment manufacturers (OEM) in the U.S. are using the Cyclone technology in demanding applications. They are reporting significant cost savings, especially in the nylon Cyclones as compared to a traditional Reservoir.”
To date, Cyclone Reservoirs have been successfully deployed in several off-highway vehicles, watercraft, military, agricultural and snow removal equipment and conveyors.
The new Cyclone Reservoirs are currently available in 10, 20 or 40 GPM roto-molded nylon or 10, 20, 40 or 60 GPM steel models. However, the ability to rapidly prototype (3D printed) nylon models allows for customized configurations in just a few days.
“With the dramatic cost savings these Reservoirs are already proving to provide I think it is safe to say they will one day become the industry norm.” says Glidden. “It is an extremely exciting development for our industry. One that has been many years in the making.”
To learn more about Cyclone Hydraulic Reservoirs visit www.cyclonehydraulics.com or call 262-709-7400.
Practical Contamination Control
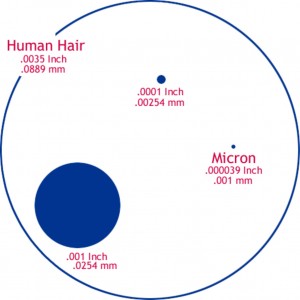
To prevent system contamination, filtration is required. This is the size of one micron, which dictates ISO standards depending on the system and it’s component parts.
Ron Durante, Price On-Site
You have heard it before: the biggest issue associated with hydraulic system failure is contamination. Over and over again it is stated, and our field service technicians confirm, that 75 to 80 percent of hydraulic problems are related to contamination. Our techs are considered hero’s simply by going out on a service call, pulling out a cartridge valve, cleaning it with brake cleaner and compressed air and reinstalling it. When in fact, 90 percent of the systems we work on don’t meet the ISO cleanliness target set forth by the manufacturer for the system’s most sensitive component. If your system operates intermittently, the prime mover operates at RPMs less than 1800 and pressures are less than 2500 PSI, you probably are not experiencing contamination related issues with your hydraulic system. But, if you’re running at higher RPMs, higher pressures, have multiple shifts and the company, along with customers, depend on this piece of equipment to be in service then do what it takes to hit your cleanliness target. Once you hit the your cleanliness target and maintain operation at this level, you can expect the system components to last three times longer. The clean, cool oil will last five times longer and you will experience a significant drop in machine downtime.
Simply put, you need to particle count to get a baseline of current contamination levels. All team members should be involved and educated so they understand the importance of correct filtration and fluid handling, training can be the most important step in the process. Help maintenance technicians understand correct fluid handling procedures and what an ISO code of 16/14/12 means. However, most of all, realize that any maintenance, no matter how careful, will introduce contamination.
Once you have a particle count baseline, you need to install the correct filters and breathers, seal up the system and most likely install a recirculation loop. After twenty-four hours, particle count again to confirm the cleanliness target is achieved. If done correctly, you will beat and never rise above the target which allows you to perform maintenance events. Remember, each time your ISO code goes up, the level of contaminates doubles. Miss it by two codes and your oil is four times as dirty. If you beat it by a code, you halved the amount of contaminates being introduced to components. Your success or failure can be measures by particle counts in an oil sample. The overall goal in a practical contamination control plan is to keep the system clean to the point that contamination is no longer a factor in component failure.
Practical contamination control is one of the least expensive way to improve the life of your hydraulic system. The associated costs are always less than equipment downtime and repairs. With contamination the causes are obvious, the solutions available, the benefits great and the return on investment is almost immediate.
7 Essential iPhone and iPad Apps for Hydraulic Troubleshooting
by: Ron Durante, Director – MRO Services
In the fluid power industry, sometimes you encounter a problem when you least expect it. You may not always have your favorite hydraulic troubleshooting tools with you when an urgent problem arises. Luckily, if you happen to have an iPhone or iPad, there is a lot you can do in a pinch.
There are plenty of apps available for a small fee (or free) that will help you find and diagnose hydraulic issues before things get out of control. Our service techs are on the road constantly and often use their iPhones and iPads to help solved simple diagnostic problems. Below are seval helpful apps/tools:
1. Big Magnify Free – iPhone and iPad
You can use this to zoom (up to 5x) in on small spaces and component features on which you need to see detail. Snap a photo and you’ve got a permanent record of a typically hard-to-find problem. It’s free and extremely useful.
2. Decibel Meter Pro ($0.99) iPhone and iPad
The first symptom of aeration or cavitation in pumps and motors is noise. This app lets you capture and see both the average decibel level and peak levels – its sensitivity also can be calibrated.
3. Hydraulic Engineer ($4.99) iPhone and iPad
Although it costs a little pocket change, this app is a worthwhile investment. It’s an all-purpose go-to app contains 60 area formulas and 300 conversion formulas for fluid power engineering. In addition, it provides you with many actuator, fluid power and hydraulic tubing formulas, pump and induction motor selection tools, and
vehicle drive formulas.
4. Metal Detector (Free) iPhone only
While working outside, it’s probable that you will drop a small part in the dirt or grass. This handy app (yes, it really works) can help you out of potentially embarrassing situations.
5. Convert Free – iPhone and iPad
No good engineer or service tech should be without a good all-purpose conversion tool. There are many others out there, but we like this one because it’s fast and you don’t need to pre-specify a category before you enter in your units. You can even save favorites and organize them into folders.
6. eSense Temperature (Free) –iPhone and iPad
Although to use this app it requires an investment in an external sensor, it is a great tool to have. You can monitor ambient temperature, oil temperature and individual component temperature at the touch of a button.
7. Eaton Powersource – iPad & web-enabled
As an Eaton distributor and authorized repair and service center, we use Powersource on a nearly daily basis. It provides you with everything from hose crimping specifications, pricing, and delivery lead times on catalog items. It also includes a comprehensive digital catalog. You can cross reference competitor’s products and also search for your local Eaton sales distributor by city, state or zip code.
Eaton’s Powersource is available to purchase from their website directly. There is a financial investment, however if you use or service Eaton products regularly, it is worth every penny.
Do you have any suggestions for hydraulic troubleshooting apps for iPhone, iPad or Android? Please add them in a comment below.
Top 10 Hydraulic Troubleshooting Tools
by: Ron Durante, Director – MRO Services
Price On-Site service technicians are out on hydraulic service and emergency calls all day, every day. It’s essential to have the right tools available to tackle any kind of problem that might arise. Whether you are a machine operator, an operations specialist, or maintenance supervisor, these tools will help you diagnose the majority of issues you may face on the plant floor and in the field. Here is my top ten list:
1. Schematics
With a good schematic you can troubleshoot over the phone and quickly diagnose possible causes to a problem by listing them in order of probability. Troubleshooting without a schematic is like trying to find an address without a map; it forces you to waste valuable time. Without a schematic, you may have to resort to random changing out of components to solve a problem.
2. The Internet
What can I say about the all-powerful Internet? Anything you want to know is just a Google search away. Many hydraulic suppliers have great information on their sites that help us out in the field. One site we like is Sun Hydraulics. They allow you to check detailed product information, schematics, download service manuals, and even gain access to 3D models.
3. Smart phones
Smart phones allow you to get free Internet access wherever there is a Wi-Fi hotspot. Taking photos and videos of machines and components can be a vital tool when diagnosing a problem in the field. FaceTime on the iPhone is an excellent tool when you need to consult someone who is not physically at the project site. There are also many great apps for iPhones and iPads that are helpful.
4. Compressed air and blowguns
These are invaluable for cleaning and inspecting, both before and after disassembly. The last thing you want to do while troubleshooting is create additional problems by allowing new contamination to enter the system.
5. Brake cleaner
We use this so often that we purchase it by the case. It works great for cleaning and inspecting parts.
6. O-ring kit
Inevitably you will be replacing seals. Sometimes an o-ring is the root cause of a problem and it’s a good practice to replace them when reassembling a component.
7. Laser heat gun
Bypassing oil causes heat. Use a laser heat gun to check relief valves for bypass, pumps for slippage, or valves for partial openings.
8. Inspection light
You must have adequate light to read component labels, as well as parts and pieces – especially in windowless and dark areas, such as in foundries and factories. A light with fiber optics is particularly useful when doing manifold tracing.
9. Allen wrench set
There are many valves you can remove and disassemble with a simple Allen wrench set. Small ones work well for operating manual overrides. I use a tiny Allen wrench on an energized coil as it becomes magnetized, because once the valve is de-energized, the Allen wrench will fall off.
10. White paper
I find it is useful have a roll of heavy weight white paper for creating a ‘clean area’ for disassembly, cleaning, inspection, and reassembly of components and parts. It keeps oil localized and visible. Furthermore, it doesn’t allow it to spread to the clean surrounding areas.
Do you think anything is missing from this list? If you have a favorite tool that you use, please share it with us!
← Older posts Newer posts →-
Archives
- August 2022
- April 2022
- August 2021
- December 2020
- August 2020
- January 2019
- September 2018
- March 2018
- February 2018
- December 2017
- November 2017
- October 2017
- September 2017
- May 2017
- April 2017
- March 2017
- February 2017
- October 2016
- September 2016
- August 2016
- July 2016
- June 2016
- March 2016
- September 2013
- July 2013
- March 2013
- January 2013
- December 2012
- November 2012
- October 2012
- September 2012
- August 2012
- July 2012
- June 2012
- May 2012
- April 2012
- March 2012
- February 2012
Signup Today
to get our monthly Enews delivered to your inbox.
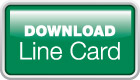