Tips for Practical Contamination Control
By: Ron Durante from Price On-Site.
Perhaps you have heard it before – the biggest issue associated with hydraulic failures is contamination.
Experts say that 75% of hydraulic problems are related to contamination.
Price On-Site has found this to be true countless times as its service technicians make service calls and solve customers’ problems with a quick solution in the field.
As a service company, we have found that 90% of the systems we work on
do not meet ISO cleanliness targets set forth by the systems’ manufacturer.
Here are some simple tips for controlling contamination in your hydraulic system:

To prevent system contamination, filtration is required. This is the size of one micron, which dictates ISO standards depending on the system and it’s component parts.
1. Meet your manufacturer’s ISO standards
Your company depends on its equipment to last a long time. With good cleanliness targets reached, you can expect component life to be three times longer, and oil life five times longer. The biggest payoff is that you will experience a significant drop in machine downtime.
If your system operates intermittently, you are probably not experiencing problems if your prime mover operates at RPMs less that 1800 and the pressures are less than 2500 PSI. But if you are running at higher RPMs, higher pressures, operate over multiple work shifts, then it is crucial that you meet your cleanliness targets.
2. Use a particle counter
One of the first simple steps is to use a particle counter to get a baseline of current contamination levels. Get the right people involved so that all can understand and address the filtration needs. Training is key.
3. Train your maintenance staff
Maintenance team members need to understand fluid handling procedures and what ISO code 16/14/12 means. They also must understand that despite extra careful measures, any service performed will introduce contamination in the system.
4. Use proper filtration methods
Using the particle count baseline as your guide, you will need to install the correct filters, breathers and possibly a conditioning loop. After 24 hours, conduct a repeat particle count and confirm that that cleanliness target has been reached and most likely exceeded to better levels. This is how a practical contamination control plan will result in keeping your system clean so that contamination will not be a cause of a component failure.
Practical contamination control is the least expensive way to improve and extend the life of your hydraulic systems. Your costs will be less and costs associated with downtime and repairs will be greatly reduced.
For more information on how to set up a contamination control plan for your hydraulic systems, contact Ron Durante, at Price On-Site. (262) 369-2147 or rdurante@priceeng.com.
More from my site
Leave a Reply
-
Archives
- August 2022
- April 2022
- August 2021
- December 2020
- August 2020
- January 2019
- September 2018
- March 2018
- February 2018
- December 2017
- November 2017
- October 2017
- September 2017
- May 2017
- April 2017
- March 2017
- February 2017
- October 2016
- September 2016
- August 2016
- July 2016
- June 2016
- March 2016
- September 2013
- July 2013
- March 2013
- January 2013
- December 2012
- November 2012
- October 2012
- September 2012
- August 2012
- July 2012
- June 2012
- May 2012
- April 2012
- March 2012
- February 2012
Signup Today
to get our monthly Enews delivered to your inbox.
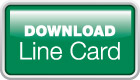